This abundance of water is a clue to why Quebec has become one of the world’s leaders in carbon-free energy. Lakes and rivers here pack enough power to supply the 7 million Quebecois with 95 percent of the electricity they need. “This country and this region really know how to run hydropower well,” says Anne McEntee, vice president for renewable energy services at GE Renewable Energy. “But there’s no reason why you cannot get even better. For decades, advances in hydro have primarily been on the physical side of things, being able to get more out of your physical assets through redesign and engineering. We are now looking at digital applications as the next advance.”
McEntee was speaking from a new office her business opened in Brossard, a Montreal suburb reachable by crossing the 2-mile-long Pont Champlain bridge over the mighty Saint Lawrence. Engineers at the office are working on software that connects hydropower plants to the internet and makes them more profitable. “Intelligent condition-monitoring applications can save as much as $4,000 per megawatt per year in reduced maintenance costs, improved asset life and higher operational efficiency,” Deb Frodl, global executive director of GE Ecomagination, and Richard Taylor, CEO of the International Hydropower Association, wrote recently. They wrote that the first customers of this “digital hydropower plant” are already “experiencing reliability improvements of 1 percent or greater.” Scaled across the world’s hydropower fleet, these savings “would amount to 413 gigawatt-hours of incremental hydro generation due to increased uptime,” they wrote. “That’s equivalent to the electrical output from over 700 wind turbines.”
[embed width="800"]https://www.youtube.com/watch?v=L8Khda7OYzM&feature=youtu.be[/embed]
The customers include the Pont Baldy power plant near GE’s hydropower headquarters in Grenoble, France. The company’s “asset performance management” software will soon start sending data from Pont Baldy to a new remote operating center on the fifth floor in the Brossard office. Large LED screens are already displaying images of the French machines and data about their operating conditions. Yet another team working next to the center is testing virtual reality simulations of power plants and other digital tools. They allow customers to walk through their plants even before they are built and make design suggestions. “This is the future,” says Daniel Paré, a 30-year veteran of the industry who works as an operational engineer in Brossard. “We are feeding digital drawings and data from the turbines into the software and creating 3D models of the machines.”
Pare was standing next to Eric Moisan, another engineer here who wore a virtual reality headset as he explored the insides of a power plant his team designed for a customer this spring. “It’s amazing because I can step inside the machine and see all the different components,” he said as he ducked down to inspect a bearing. “It allows us to see problems that could be hard to find, like leaving enough space for the maintenance crew to service tight spots. We can also walk customers through the design instead of showing it to them on a piece of paper or a computer screen.”
The GE hydro turbines installed around the world can produce 350 gigawatts today. But they also are aging, approaching 40 to 50 years old on average. The good news is that many of the machines are already equipped with sensors that can measure power, temperature, vibrations and other data, says David Tessier, the engineer running the remote operating center in Brossard. “In the past, we had a bunch of information, but we weren’t able to integrate it,” he says. “But our new software allows us to observe how the physical components behave in real time.”
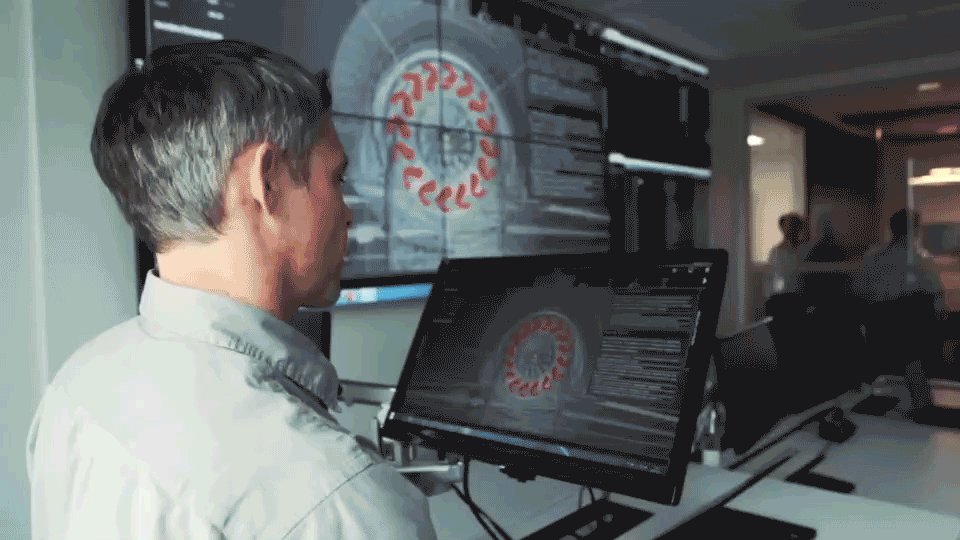
McEntee says the insights allow customers to adapt the turbine’s operations to the specific conditions on-site, rather than strictly follow the manual. “We can take into account the real water and flow conditions versus what it was designed to do,” she says. “This allows us to make use of the error tolerance and get more power when we need it, like when the price is favorable. We are constantly looking for opportunities to squeeze out 1, 2, 3 percent of efficiency.”
The GE team can do that because the system creates a virtual representation of the hydropower plant in the cloud, its “digital twin,” and uses the data to compare it to real-world conditions. “The idea is to theoretically model what the perfect turbine should do, and then adjust the running conditions over time as the data comes in,” McEntee says. It can also point designers to new ideas. “The goal is to constantly revalidate what it takes to produce those turbines and make them better.”
Besides Pont Baldy, a version of the system is already running at another hydropower plant in France, and the company has plans to roll it out in Bhutan and in the U.S.
McEntee has high hopes for the industry. Hydropower is not only a carbon-free way to generate large amounts of power on demand, but in the absence of grid-scale batteries, it also can help utilities bring more renewable power online by bridging the gap when the wind stops blowing or the sun hides behind a cloud. “I think the future is extremely bright,” she says, adding that each new generation of engineers entering the industry is technologically savvier than the one that came before.
Says McEntee: “There’s no doubt that with advances in software and analytics, virtual reality and 3D printing, which allows you to make designs previously out of reach, the future of hydro is digital.”
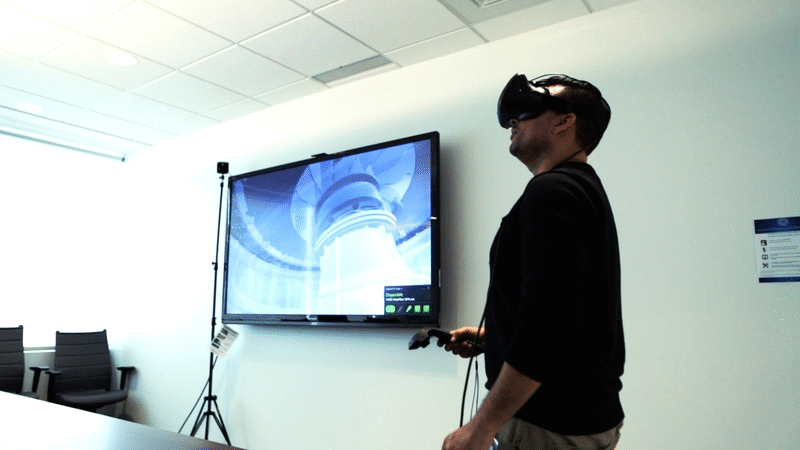